Zamac
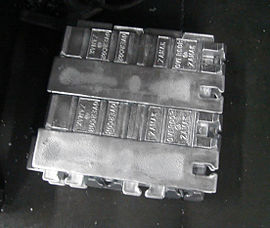
Zamac is the generic name for several metallic alloys with a melting point between 385 °C and 485 °C, basically containing zinc (Zn), together with aluminum (Al), magnesium (Mg) and copper (Ass). The name comes from Z ink- A luminium- Ma gnesium- K upfer (zinc, aluminum, magnesium and copper, in German, respectively). [ 1 ]
Overview
In industry, several Zamac alloys are used, with different levels of Al, Mg and Cu, which results in different mechanical properties. They are low-cost materials used in the casting of parts that require little mechanical resistance. The material in liquid state is injected under pressure into steel or silicone rubber molds in the shape of the parts to be produced. [ 2 ]
Zamac's technical applications include: carburetors for automobiles, pressure regulating valves for gas cylinders and accessories for electrical installations (bushings, junction boxes, curves, etc.). It is also used in handles for cabinets and drawers, door handles, key chains, jewelry, toys, buckles for clothes and shoes, decorations for clothes, bags and shoes.
Standards
There are several standards that define the compositions and properties of zinc alloys, the main ones below:
Country | Zinc Ingot | Zinc Casting |
---|---|---|
Europe | EN1774 | EN12844 |
USA | ASTM B240 | ASTM B86 |
Japan | JIS H2201 | JIS H5301 |
Australia | AS 1881 - SAA H63 | AS 1881 - SAA H64 |
China | GB 8738-88 | - |
Canada | CSA HZ3 | CSA HZ11 |
BRAZIL | ASTM B86 - 13 |
Zamac 2
Zamak 2 or Kirksite is the commercial name of a league in zinc - aluminum frequently used for the production of tools and molds (especially for plastic injection and stamping of thin steel parts).
Characteristics
Kirksite molds and tools are low cost due to the ease of machining and finishing the tool surface. Another main characteristic of Kirksite is that it can be melted at a temperature of 400 °C indefinitely, losing very little of its mechanical characteristics. Easy machinability is also another highlight of Kirksite.
Therefore, it is ideal for making tools for developing prototypes on a low production scale or permanent molds for high-value-added parts in PE, PP, ABS whose expected production does not exceed a few tens of thousands of pieces.
applications
Typical applications for Kirksite alloys are:
- Molds for the manufacturing industry rubber and from ceramics .
- Stamping tools for low production volume parts.
- injection molds plastic .
Alternative that replaces steel in the production of injection molds. Cast using the ceramic casting process, they eliminate costs and, above all, time when compared to the production of CNC-machined steel molds. The use of molds built in Kirksite is especially recommended for large parts that require relatively low injection pressures.